La TPK-Kunststofftechnik di Nörten-Hardenberg, vicino a Göttingen, è specializzata nella produzione di sofisticati articoli in plastica e stampi a iniezione. Fondata nel 1997 e gestita da Werner Ternka e dai suoi figli Heiko e Mario, l'azienda a conduzione familiare ha circa 30 dipendenti e si occupa dell'intera catena di processo: dalla consulenza, progettazione, costruzione di utensili e produzione di prototipi allo stampaggio a iniezione in serie e al montaggio.
Le esigenze di qualità dei pezzi stampati a iniezione sono aumentate negli ultimi anni, sottolinea Mario Ternka, responsabile dello sviluppo dei prodotti, del design e della costruzione degli stampi alla TPK-Kunststofftechnik: "I dati dei disegni che riceviamo dai nostri clienti contengono oggi molte dimensioni e tolleranze che non possono essere misurate con gli strumenti di misurazione manuali convenzionali e con apparecchi di misurazione più semplici, per esempio le tolleranze di forma e di posizione, come ortogonalità, parallelismo e planarità, o le tolleranze di forma libera. Per misurare correttamente questi criteri, abbiamo bisogno da un lato di un hardware adatto, ma anche di un buon know-how che traduca i valori misurati nel linguaggio della costruzione degli stampi. Pertanto, non possiamo lasciare la misurazione a un fornitore di servizi metrologici".
TPK soddisfa i maggiori requisiti di qualità con una metrologia all'avanguardia
Così TPK ha deciso di investire in un'attrezzatura di misura adeguata. Sulla base di una scheda tecnica di 60 punti, un team di specialisti ha valutato le offerte di noti produttori di strumenti di misura e ha deciso di acquistare una macchina di misura a coordinate multisensore ScopeCheck® FB 3D della Werth Messtechnik.
Il suo design con un cavalletto fisso su una base di granito e le robuste guide meccaniche di precisione assicura una precisione molto elevata, anche quando viene utilizzata durante la produzione. L'attrezzatura comprende un sensore di elaborazione delle immagini grazie a Werth Zoom e un'unità di illuminazione multi-ring supplementare per il rilevamento rapido e affidabile dei bordi, oltre al tastatore di scansione SP25. Inoltre, la scansione raster viene utilizzata per generare immagini complessive ad alta risoluzione a partire da singole immagini catturate mentre il sensore è in movimento. Con queste, le misurazioni possono essere comodamente eseguite. Per una rapida misurazione ottica delle superfici, TPK ha investito anche nel sensore di distanza CFP, che utilizza l'aberrazione cromatica di lenti speciali per misurazioni estremamente accurate e indipendenti dalla superficie.
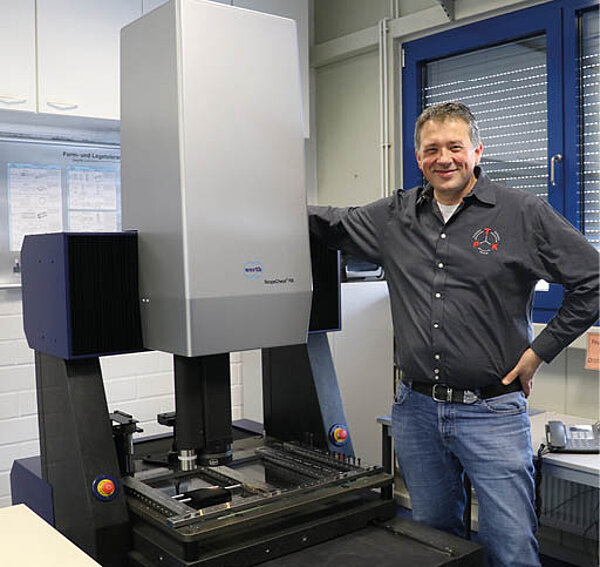
Mario Ternka è entusiasta della Werth ScopeCheck® FB: "In particolare, prima non avremmo ritenuto possibile precisione e velocità dei sensori ottici".
"In cima alla lista dei nostri requisiti c'era la combinazione di capacità di misurazione ottica e tattile", spiega Ternka. "E il sensore di distanza ottico doveva fornire risultati di misurazione affidabili per parti lucide, trasparenti, nere o bianche".
Lui e i suoi colleghi sono particolarmente entusiasti della tecnologia del sensore ottico della ScopeCheck® FB: "Non avremmo mai pensato che precisione e velocità fossero possibili prima. Questo è stato il fattore decisivo a favore della ScopeCheck. Il dispositivo può anche essere programmato rapidamente e facilmente - dopo solo un breve periodo di formazione. La misurazione e la valutazione avvengono poi in modo completamente automatico".
ScopeCheck® come elemento importante nella catena di processo alla TPK
Lo stampaggio a iniezione è un processo di formatura primario in cui i criteri di qualità come le tolleranze di forma e posizione ecc. sono molto più difficili da mantenere che nella lavorazione. Richiede un grande know-how produttivo e una catena di processo come quella che TPK ha sviluppato e ottimizzato negli ultimi anni.
All'inizio di questa catena di processo c'è il modello CAD 3D. Con questo, i progettisti creano un primo stampo virtuale e una simulazione di stampaggio a iniezione. Da un lato, i risultati dell'analisi vengono utilizzati per ottimizzare l'oggetto, e dall'altro per migliorare lo strumento di stampaggio. In questo modo, gli ingegneri plastici cercano di contrastare le difficoltà dello stampaggio a iniezione - soprattutto le distorsioni causate dal ritiro longitudinale e trasversale.
"Già nella fase di progettazione dello stampo a iniezione dobbiamo prendere in considerazione i percorsi di flusso della plastica, prevedere il controllo della temperatura e i canali di raffreddamento, e pianificare la sformatura e la rimozione del pezzo", spiega Ternka. La simulazione ripetuta fornisce informazioni sul sistema a canale caldo appropriato, sul punto di iniezione ottimale, sulla posizione dei canali di raffreddamento, sulle tolleranze, sulla bombatura e molto altro. Solo quando gli specialisti dello stampaggio a iniezione sono sicuri che il design dello stampo si adatta all'insieme producono lo stampo in acciaio. Alla TPK, questo viene fatto principalmente su macchine utensili moderne, per esempio tramite fresatura ed erosione a 5 assi.
Nei casi più semplici, la precisione dimensionale di utensili di formatura complessi viene misurata direttamente sulla macchina utensile. Misurazioni difficili, come quella della posizione di un contorno rispetto ai bordi esterni, possono essere eseguite dagli attrezzisti grazie alla Werth ScopeCheck® FB e alla combinazione della tecnologia dei sensori ottici e tattili.
Una volta che lo stampo è pronto, viene campionato su una delle 15 macchine di stampaggio a iniezione con forze di serraggio fino a 2.200 kN e ulteriormente ottimizzato nell'officina stampi fino a quando lo stampaggio a iniezione e la sformatura sono stabili. Il progettista TPK crea quindi, sulla ScopeCheck®, un programma di misurazione su un pezzo campione che registra tutti i criteri decisivi. In base ai risultati, vengono decise ulteriori modifiche da applicare allo stampo. Dice Ternka: "In questa fase, di solito parliamo di correzioni nell'ordine di qualche decimo o centesimo di millimetro, che sono necessarie per mantenere tolleranze molto strette. Senza la precisione della nostra macchina multisensore, non saremmo in grado di registrare tali valori, se non con grandi spese".