TPK-Kunststofftechnik GmbH w Nörten-Hardenberg koło Getyngi specjalizuje się w produkcji zaawansowanych artykułów z tworzyw sztucznych i form wtryskowych. Założona w 1997 roku rodzinna firma, zarządzana przez Wernera Ternkę oraz jego synów Heiko i Mario i zatrudniająca około 30 osób, obejmuje cały łańcuch procesów: od doradztwa, projektowania, produkcji narzędzi i prototypów po seryjne formowanie wtryskowe i montaż.
Do klientów firmy należą przede wszystkim firmy z branży medycznej, laboratoryjnej i motoryzacyjnej, które znane są z bardzo wysokich standardów jakości. Wymagania te wzrosły jeszcze bardziej w ostatnich latach, podkreśla Mario Ternka, odpowiedzialny za rozwój produktu, projektowanie i konstrukcję form: "Dane rysunkowe, które otrzymujemy od naszych klientów, zawierają wiele wymiarów i tolerancji, których nie można zmierzyć za pomocą konwencjonalnego ręcznego sprzętu pomiarowego i prostszych urządzeń pomiarowych, na przykład tolerancji kształtu i położenia, tj. prostopadłości, równoległości i płaskości, a także tolerancji swobodnego kształtu. Aby prawidłowo zmierzyć te kryteria, potrzebujemy z jednej strony odpowiedniego sprzętu, ale także dużej wiedzy specjalistycznej, która przekłada zmierzone wartości na język produkcji form. Dlatego nie możemy pozostawić pomiarów dostawcy usług metrologicznych".
TPK spełnia zwiększone wymagania jakościowe dzięki najnowocześniejszej technologii pomiarowej
Firma TPK postanowiła więc zainwestować w odpowiedni sprzęt pomiarowy. Korzystając z 60-punktowego arkusza specyfikacji, zespół specjalistów TPK ocenił oferty znanych producentów sprzętu pomiarowego – i zdecydował się na zakup wieloczujnikowej współrzędnościowej maszyny pomiarowej ScopeCheck® FB 3D z Werth Messtechnik na Giessen.
Jej konstrukcja ze stałym mostem na granitowej podstawie i solidnymi, mechanicznymi prowadnicami precyzyjnymi zapewnia maksymalną dokładność, nawet gdy jest używana blisko produkcji. Sprzęt obejmuje czujnik przetwarzania obrazu z Werth Zoom i dodatkową wielopierścieniową jednostką oświetlającą do szybkiego i niezawodnego wykrywania krawędzi, a także sondę skanującą SP25; ponadto skanowanie rastrowe służy do generowania ogólnych obrazów o wysokiej rozdzielczości z pojedynczych obrazów wykonanych podczas ruchu czujnika, które można następnie wygodnie zmierzyć. W celu szybkiego optycznego pomiaru powierzchni, TPK zainwestowało również w czujnik odległości Werth CFP, który wykorzystuje aberrację chromatyczną specjalnych soczewek do niezwykle dokładnych i w dużej mierze niezależnych od powierzchni pomiarów.
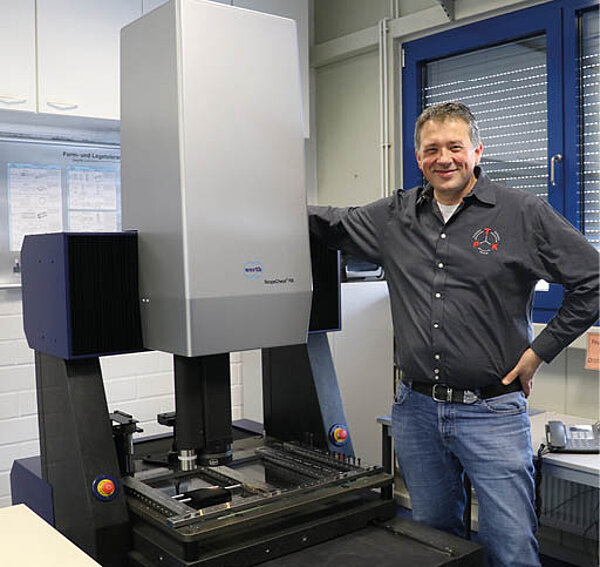
Mario Ternka jest zachwycony systemem Werth ScopeCheck® FB: "Nigdy wcześniej nie pomyślelibyśmy, że dokładność i szybkość czujników optycznych jest możliwa".
Ale jak zapadła ta decyzja? "Połączenie optycznych i dotykowych opcji pomiarowych było na szczycie naszej listy wymagań", wyjaśnia Mario Ternka. "A optyczny czujnik odległości musiał zapewniać wiarygodne wyniki pomiarów dla części o wysokim połysku, przezroczystych, czarnych lub białych".
Ternka i jego koledzy są pod szczególnym wrażeniem technologii czujnika optycznego Werth ScopeCheck® FB: "Wcześniej nie pomyślelibyśmy, że dokładność i szybkość są możliwe. To był ostateczny czynnik decydujący na korzyść ScopeCheck®." Podkreśla również jego dostępność i łatwość obsługi: "Urządzenie można zaprogramować – szybko i łatwo po niewielkim szkoleniu –. Pomiar i ocena przebiegają wtedy w pełni automatycznie".
Werth ScopeCheck® jest ważnym elementem w łańcuchu procesów TPK
Formowanie wtryskowe jest podstawowym procesem formowania, w którym kryteria jakościowe, takie jak tolerancje kształtu i położenia itp. są znacznie trudniejsze do spełnienia niż w przypadku obróbki skrawaniem. Wymaga dużej wiedzy specjalistycznej w zakresie produkcji i łańcucha procesów, który firma TPK opracowała i stale optymalizowała w ostatnich latach.
Łańcuch procesów rozpoczyna się od modelu 3D CAD. Projektanci wykorzystują go do stworzenia wstępnej wirtualnej formy i symulacji formowania wtryskowego. Wyniki analizy są wykorzystywane z jednej strony do optymalizacji artykułu, a z drugiej do ulepszania narzędzia do formowania. W ten sposób inżynierowie tworzyw sztucznych starają się przeciwdziałać trudnościom związanym z formowaniem wtryskowym –, w szczególności zniekształceniom spowodowanym skurczem wzdłużnym i poprzecznym –.
"Projektując formę wtryskową, musimy wziąć pod uwagę ścieżki przepływu tworzywa sztucznego, zapewnić kontrolę temperatury i kanały chłodzące oraz zaplanować rozformowanie i usunięcie części" - wyjaśnia Mario Ternka. Powtarzana symulacja dostarcza informacji na temat odpowiedniego systemu gorących kanałów, optymalnego punktu wtrysku, położenia kanałów chłodzących, naddatków, zwieńczenia i wielu innych. Dopiero gdy specjaliści od formowania wtryskowego są pewni, że projekt formy jest ogólnie odpowiedni, produkują formę stalową. W TPK odbywa się to głównie na nowoczesnych obrabiarkach, np. poprzez 5-osiowe frezowanie i erodowanie.
W prostych przypadkach dokładność wymiarowa złożonych narzędzi do formowania jest mierzona bezpośrednio na obrabiarce. Trudne pomiary, takie jak położenie konturu w stosunku do zewnętrznych krawędzi i położenie wgłębień w kieszeni lub toczonych rdzeni, mogą być wykonywane przez producentów form przy użyciu Werth ScopeCheck® FB oraz kombinacji technologii czujników optycznych i dotykowych.
Gdy forma jest gotowa, jest ona próbkowana na jednej z 15 wtryskarek o sile zamykania do 2200 kN i dalej optymalizowana w dziale produkcji narzędzi, aż do uzyskania stabilnego formowania wtryskowego i rozformowywania. Następnie projektant TPK tworzy program pomiarowy na próbce uformowanej wtryskowo na ScopeCheck®, który rejestruje wszystkie decydujące kryteria. Dalsze zmiany w formie są podejmowane na podstawie wyników. Mario Ternka podkreśla: "W tej fazie mówimy zwykle o korektach w zakresie od kilku dziesiątych do setnych części milimetra, które są niezbędne do spełnienia bardzo wąskich tolerancji. Bez precyzji naszego wieloczujnikowego urządzenia nie bylibyśmy w stanie rejestrować takich wartości lub byłoby to bardzo kosztowne".